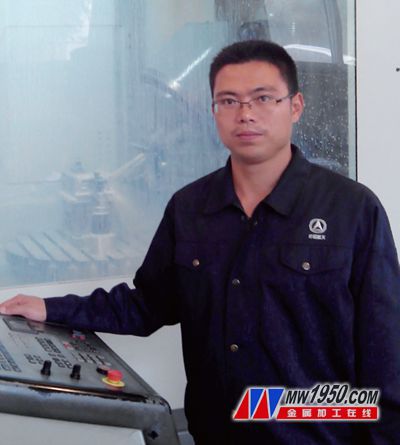
Feng Hao, Beijing Institute of Control Engineering
There are many difficult-to-machine materials in the processing of aerospace products, such as titanium alloys, high-temperature heat-resistant materials, stainless steel and hard alloys. These materials are processed by traditional metal cutting machines, which are not only inefficient, but also costly and expensive. Some materials can't even be processed at all. There are also many parts with complex shapes, such as narrow slits, narrow grooves, machining locations that cannot be completed with complex spatial positions, and micro-holes that are incapable of using traditional machining methods. These have become "bottlenecks" in the processing of aerospace parts.
The electric machining technology not only realizes the processing of hard, brittle, tough, sticky and other difficult-to-machine materials, but also realizes efficient and low-cost processing.
At present, our electrical processing technology is mainly used in the filter liquid filter, housing, manifold, guide springs, springs, micro holes and special-shaped hole parts. With the development of modern manufacturing industry, the processing precision and efficiency are constantly improving. Many high-precision and complex parts in aerospace products use traditional metal cutting processing with low efficiency and low qualification rate, which is difficult to adapt to the needs of space missions. However, if the machining process is improved, many problems with the electrical machining technology will be solved. Here are a few typical cases to explore the advantages of electrical machining technology in improving part accuracy, surface quality and processing efficiency.
1. Case 1: Using wire cutting technology to solve the problem of slender hole processing
The parts shown in Figure 1 are made of:
1Cr18Ni9Ti, outer diameter 10.5 mm, inner diameter

The total length is 23.5 mm. According to the design requirements, the diameter of the inner hole

Dimensional tolerances must meet the pattern requirements. Therefore the diameter of the inner hole
Become a difficult part of the processing of this part. Difficulties: The material is difficult to process materials.
1Cr18Ni9Ti is austenitic stainless steel, which has many factors such as high toughness, high thermal strength, low thermal conductivity, hardening during processing and difficulty in heat dissipation. It leads to high cutting temperature at the tip and easy to produce built-up edge, which not only aggravates the tool. Wear and tear, which affects the surface roughness of the part.
Difficult point two: small hole, high dimensional accuracy.
Inner diameter

Directly using the drilling method can not achieve the dimensional accuracy requirements of the pattern. The turning and boring method is adopted. Since the hole diameter ratio is larger than 5, the diameter of the boring tool must be less than 4 mm, the strength is low and the cutting edge wear is serious, and the dimensional accuracy and surface cannot be ensured. Roughness. The hole has been machined by turning, first drilling with a φ 3.8 mm drill bit, then reaming with a reamer, each time before reaming, a new reamer is required to test the hinge, and then the reamer is manually ground to find the cutting parameters. This processing efficiency is extremely low, each processing takes about 2 hours, and the inner hole processing is prone to taper, and the pass rate is only about 30%. For a long time, it can only be guaranteed by multi-production.
In order to ensure that the part processing meets the design requirements of the drawings, after several tests, the parts are required to be φ 10.5 mm and 23.5 mm in length according to the drawings, and the dimensional consistency is guaranteed to be within 0.02 mm, and the inner hole is opened with a φ2 mm drill bit. Wire-cutting holes. Then, use the clamp to clamp the outer circle and use the slow wire to cut the inner hole. The test results show that the method of using slow wire cutting is very good to ensure the dimensional accuracy and dimensional consistency of the parts. After the metering inner hole diameter is 4.09 mm, the inner hole surface roughness value is 0.825 mm, and the inner hole diameter uniformity performance is controlled within 0.002 mm. The wire cutting time is 30 min per piece, the processing cycle can be shortened by 50%, and the pass rate can reach over 98%. Therefore, the use of slow wire processing can ensure that the inner hole diameter dimension tolerance meets the requirements of the pattern, improve the part processing qualification rate, and improve the part processing efficiency.
2. Case 2: EDM to solve the problem of component routing burrs
The parts shown in Figure 2 are welded from two different materials, with 1.5 mm × 3 mm and 1.5 mm × 3.5 mm wire troughs in the middle two sections, φ 1.5 mm through-hole wiring holes, wire holes and The processing of the wire trough can only be carried out after the single piece roughing of the segment. Since the burrs are turned into the wire trough and the hole during the finishing of the part, the removal of the wire trough and the hole burr has been used by the fitter for a long time. The chamfering is completed. Since the distance between the two sections is only 5 mm (see Figure 2), the space of the file is narrow, which causes the parts to be scratched during the process of repairing the deburring (see Figures 3 and 4).
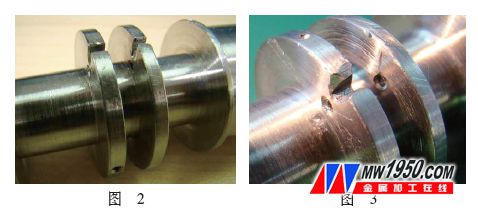
It can be seen that the manual repairing the cable trough and the hole have the following disadvantages: 1 The surface quality of the part is not easy to control during the repair process, and it is easy to cause the surface of the part to be scratched. 2 manual repair deburring efficiency is low. 3 manual repair cable trough chamfer consistency can not be guaranteed. 4 After the manual deburring, it is easy to cause secondary burrs.
According to the structural characteristics and machining characteristics of the parts, it is proposed to use the EDM method to remove the burrs of the 1.5 mm × 3 mm and 1.5 mm × 3.5 mm wire troughs and the edge of the φ 1.5 mm wire hole. The shaped electrode shown in Fig. 6 was designed and processed according to Fig. 5.
Through the process test, it shows that the burrs of the 1.5 mm × 3 mm and 1.5 mm × 3.5 mm wire grooves and the φ 1.5 mm wire hole edge are processed by EDM to remove the following advantages: 1 The deburring process of the part is controllable and does not cause scratches on the surface of the part. 2 greatly reduced the labor intensity. 3 The operation process is controllable, time-saving and efficient, and the processing efficiency can be increased by more than 50%. 4 can guarantee the consistency of chamfering processing, suitable for batch production of parts. The effect of using EDM is good, and the effect after processing is shown in Fig. 7 and Fig. 8.
3. Case 3: Using EDM to solve the problem of part milling
The part shown in Fig. 9 is a high-precision important part of the solar sensor that carries the optical head. The two trapezoidal through holes have a rectangular window of 50 mm × 41 mm. Through the milling of all other shapes, the design pattern can be achieved. Only the rectangular window of 50 mm × 41 mm in the middle can be processed into the shape shown in Fig. 10 only by the T-knife.
According to the process requirements, there is a separate process for processing the sharp corners of the rectangular window up and down with a special T-shaped cutter on a common milling machine. If the milling method is used, the T-knife can not be processed directly. The handle of the special T-knife must be passed from the trapezoidal cavity through the connector window at the bottom (see Figure 11). Go to the spindle of the machine. At the time of processing, it must also be ensured that the side edge of the T-knife cannot touch the side. To process one piece, it is necessary to change the tool at least twice. Therefore, the processing efficiency is not only low, but also it is difficult to ensure the pattern size requirement.
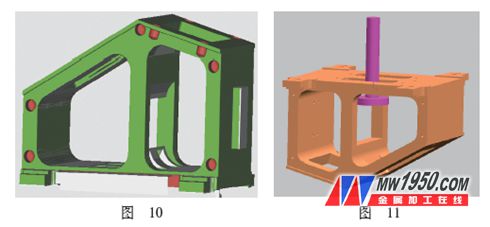
In order to meet the design pattern requirements, it was decided to use the EDM technology to process the rectangular window. The dimensions shown in Figure 1 2 are:
The material is a copper-shaped EDM electrode. Figure 13 is a photograph of a window of a window processed using an EDM electrode. Tests show that the switch to EDM is completely feasible and has the following advantages: 1 convenient and efficient. Just look for the first piece, basically do not need to repeat the correction, suitable for small batch production. 2 processing costs are low. The cost of the copper electrode used is lower than that of the alloy tool, and the electrode loss is small and can be reused. 3 dimensional consistency is guaranteed, which can improve the part qualification rate. Reduce the dependence of part processing on the skill level of the operator, and align the workpiece. As long as the parameters are set properly, correct operation can ensure the parts are qualified.
4. Conclusion
Through the above typical case analysis, with the rapid development of electric machining technology, many problems that are difficult to solve by traditional metal cutting processing can be solved with modern electric machining technology. Practice shows that electrical machining can not only improve the processing yield and surface quality of parts, but also improve processing efficiency and reduce costs. Therefore, we must continue to innovate, develop ideas, use the advantages of electrical processing technology combined with advanced metal cutting technology to develop efficient, high-quality processing solutions, improve the processing accuracy and qualified rate of parts, in order to ensure the high reliability of aerospace products.
When cable suffers form aeolian vibration, the hammerhead of the vibration Damper hanging on the cable may vibrate freely along with the movement of cable to make the steel stranded wires on anti- vibration damper rub each other, convert the vibration energy passed on to the anti- vibration damper to friction heat among steel standed wires and consume such heat energy, thereby effectively supperessing the aeolian vibration of cable and prolongthe life of cable.
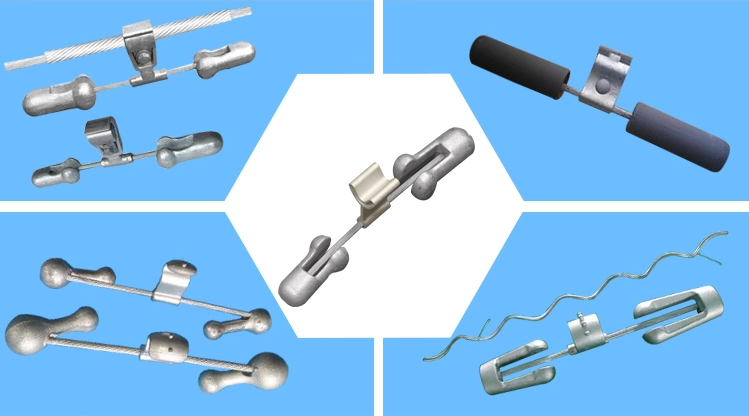
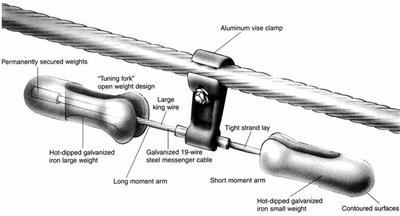
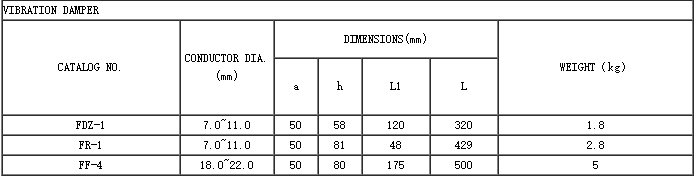
If you have any questions, please contact with us directly.
Our company is solemnly committed to the majority of customers: reasonable price, short production cycle, considerate service. We look forward to cooperating with you.
Damper
Vibration Damper,Fr Vibration Dampers,Fd Vibration Damper,Fdz Type Damper
Shandong Vantage International Trade Co., Ltd. , https://www.steelplate.be