Honeywell Aerospace is one of Honeywell's largest multinational companies in commercial and residential engineering, producing a wide range of impellers and leaf discs for commercial aircraft.
The impeller is essentially a combination of a radial compressor and an axial compressor. In the process of machining the impeller, it is necessary to always ensure that the workpiece reference position is correct, so as to ensure that a qualified product is processed.
If the workpiece reference position is deviated, the machined impeller will not meet the specifications. At this time, it can only be reworked or repaired, and may even be completely scrapped.
In order to maintain the accuracy of the process, Honeywell turned to Renishaw, a multinational company in the engineering field, which provided the RMP600 high-precision machine tool probe measurement system and computer-based Productivity+TM workpiece measurement software for its machining center. Honeywell can now use Renishaw products to perform pre-sequence measurements and sequential axial displacement detection.
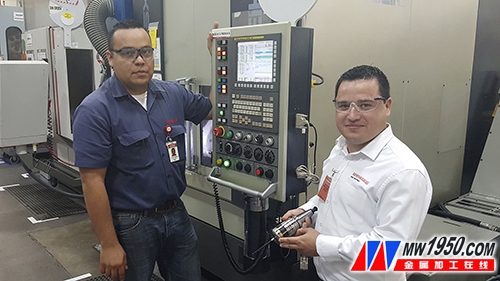
Luis Adrián Gallegos, production engineer at Honeywell Aerospace, and Gilberto Ochoa, application engineer at Renishaw
background
Honeywell manufactures impellers at its plant in Chihuahua, Mexico. The plant is equipped with the latest machinery to perform parts grinding, milling, turning and drilling.
The impellers produced here range in diameter from 14 inches to 17 inches. Most impellers are made of titanium alloy and only one impeller is made of aluminum alloy.
Products from the Chihuahua plant are sent to Honeywell's assembly plant in Phoenix, Arizona, USA, where the main job is to assemble and test turbines for aero engines.
If the workpiece reference position of the finished part is found to be off center, it must be submitted to the product design department where the designer checks the impeller and determines compliance.
The cost per analysis for each workpiece is approximately $66,900, which also increases overall manufacturing time. The machining time per impeller (including the clamping time in the machine) can take up to 60 hours and approximately 130 tools are used.
In Honeywell, the production time for a single impeller is planned to be two weeks. If the workpiece is found to be off-center after machining, it takes an additional week to perform the necessary analysis, which will result in machine downtime and production delays, which will have a negative impact on production time and manufacturing costs.
challenge
“In the process of impeller machining, Honeywell found that the workpiece reference often deviates in the axial direction, which can lead to prolonged machining time of the workpiece,†said Raúl Barriga, Sales Director of Renishaw Mexico.
Axial displacement of the original center point may be caused by incorrect workpiece alignment, which may be caused by operator error, fixture damage, and/or burrs remaining on the workpiece in the previous process.
solution
After completing the first impeller manufacturing, Honeywell's production engineer Luis Adrian Gallegos sat with other quality control engineers to discuss how these benchmark deviations could be reduced during processing.
“After the first production cycle is completed, we know we have to improve the process, but we don’t want to invest too much money,†Gallegos said. “We contacted Renishaw to discuss whether high-precision ultra-small triggering can be used. Head and, in conjunction with Renishaw software, measure the workpiece before machining begins and detect any baseline deviations to correct them in advance."
“After evaluating Renishaw's range of probes, we decided to purchase the RMP600 machine probe with radio signal transmission. This probe has all the advantages of automatic workpiece alignment and is able to measure the geometric characteristics of complex 3D workpieces. Like our impeller."

Renishaw RMP600 high precision trigger probe
During the machining process, the Renishaw probe can touch the workpiece from various positions to determine if there is any error or collimation deviation.
“The probe can help us detect all potential problems before they actually occur,†Gallegos added. “In the past, we were able to find any problems until 16 hours of processing and more than an hour of measurement. Now, we can immediately get the alarm information of the workpiece size and position deviation from the probe and take necessary corrections, thus avoiding wasting valuable processing time and resources."
“In addition to the probes, Honeywell purchased the computer-based workpiece measurement software Productivity+ for its machining centers. This software provides Honeywell with an easy-to-use programming environment for the workpiece inspection probe program and The in-sequence correction program is integrated into the machining cycle. Productivity+ helps to simplify the workpiece alignment and inspection process, and can be used in the core machining process: workpiece identification and alignment, tool identification and tool setting. Productivity+ also helps to generate the sequence. Post-report, which collects completed process information and helps to make decisions for subsequent processes,†Barriga commented.
result
“Since we started using the RMP600 touch probe and the Productivity+ workpiece measurement software, we have never had any problems with workpiece overrun, rework or scrap,†Gallegos said. “The software can assist in the process. Control tasks, such as monitoring the status of the tool based on data collected by the probe, updating the tooling and completing the adaptive machining."
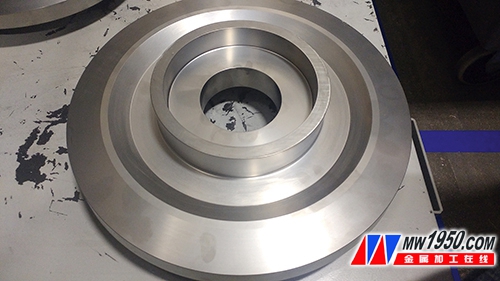
Pre-processed _ uncut raw blank
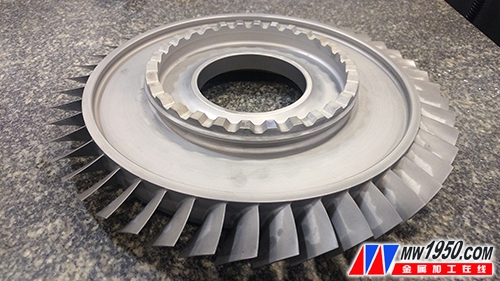
After processing _ finished leaf disc
“With Renishaw's probes and software, Honeywell can ensure that the machining process does not deviate. Before introducing Renishaw's new technology, the machine operator must first fix the workpiece on the machine, manually measure it, and then Enter the diameter and surface position data into the controller. If there is any omission or error in the information, or the fixture is damaged, the final processed product will be unqualified. Now, we can eliminate any defects by pre-sequence detection. occur."
“Although some workpieces are inevitably required to be reworked after processing for various reasons, this does impose an additional financial burden on the company. By receiving real-time data from the Renishaw in-cam measurement system, we are able to Feedback to adjust the machining process, which helps to minimize the chance of repeated occurrences of the same problem on multiple workpieces. Renishaw's equipment has helped us improve the machining process and reduce machine downtime for our one-time success 'Processing the impeller used in the modern aerospace industry has laid a solid foundation,†concludes Gallegos.
Adapted from "Modern Machine Shop Mexico" magazine, has been officially authorized by the original editor
For more information, please visit
-Finish-
Product Information
Product Name
|
Home used brass chrome plated bath square Shower Head holder
|
Items No.
|
customized
|
Material
|
59% brass
|
Type
|
Shower head holder
|
Surface Treatment
|
Chrome plated
|
Guarrantee
|
5 years
|
|
Packaging & Delivery
Packaging DetailsHome used brass chrome plated bath round shower head holder
Inner packing:
cloth bag, white color or craft inner box,
Outer packing:
Kraft carton,
The package can be done as customers' requirements.PortJiangmen, Guangzhou, Shenzhen
Square Brass Shower Holder
Square Brass Shower Holder,Adjustable Shower Head Holder,Brass Held Shower Holder,Square Brass Bathroom Shower Holder
KaiPing HuiPu Shower Metalwork Industrial CO,LTD , https://www.hp-shower.com