In the aircraft body assembly design/manufacturing process, a large number of fastener-related geometric and non-geometric information needs to be defined and used. In addition to the need to generate a three-dimensional geometric model, the assembly design needs to attach the attribute information and connection information of the fastener to the three-dimensional geometric model to generate a complete three-dimensional digital product definition, and then deliver it to the manufacturing workshop. Traditionally, using general-purpose software, engineers need to manually define and obtain tens of thousands of fastener information, including fastener grades, fastener placement locations, and more. This is a cumbersome, error-prone and time-consuming task, and in many cases these tasks are not automatic or are not well supported by 3D CAD systems. At the same time, engineers must accurately use specifications to efficiently define the different stages of the manufacturing process to ensure that the final product meets engineering requirements. This complexity, along with increasing market demands and the pressure to bring products to market quickly, poses a huge challenge to engineers and the software tools they use.
With the further development of China's large passenger aircraft project, the full three-dimensional design technology of aircraft structure has achieved revolutionary development and application. The structural design has entered the full 3D era, replacing the traditional 2D drawings and realizing the paperless design of the whole process. . The only basis for designing and manufacturing MBD data sets poses new challenges to traditional manufacturing methods and methods. Based on MBD technology, geometric and non-geometric information definitions related to aircraft body assembly design are combined, and a new three-dimensional fastener assisted design system is developed in combination with the new idea of ​​fasteners online association full information expression. The installation of fasteners has changed from the problem that originally plagued the design and manufacturing departments to the power and hub that drives the assembly design, improving the efficiency and quality of each link. Based on the above application background, this topic mainly realizes the key technology research and software system development of fastener auxiliary system based on full three-dimensional design.
key technology research 1. Research on design standards and modeling specifications based on full three-dimensional fasteners
Through research, we have determined a series of design specifications and standards from fastener selection, transfer, installation, calculation analysis and inspection; breaking through the traditional assembly design of fasteners, using the full information skeleton feature line to express The method of fasteners.2. Research on fastener method based on MBD technology
The format and position of fastener-related geometric and non-geometric information stored in CATIA model based on MBD technology are studied. The design standards and specifications based on MBD technology are determined, which provides the basis for later system implementation.3. Research on knowledge-based fastener association method
The matching and related combination relationship between commonly used fasteners are studied, and the technical specifications of fastener associations are clearly defined, such as the matching relationship of bolts, nuts, washers and insurance pins of different grades, the use environment and process specifications. Etc., and the determined rules are embedded in the system database to facilitate the system implementation, breaking through the traditional way of looking up the table, realizing the automatic matching and filtering of the fastener association combination.System implementation
Based on the results of key technology research, a fastener-assisted system CAFE based on full three-dimensional design based on the development of large passenger aircraft was developed. The system uses knowledge engineering technology to refine and solidify aircraft body assembly design knowledge and experience, providing a unified working environment for aircraft structural designers and manufacturing personnel. Using MBD specification and related technology to intelligently define the assembly information quickly, generate a full 3D digital product model, transfer it to the manufacturing unit, extract the manufacturing information based on the unified full 3D digital product model, and cancel the 2D drawing release. Seamless integration and efficient collaboration between design and manufacturing.
The CAFE system is a rapid design system based on the combination of B/S and C/S. Based on the fastener database, the aircraft fasteners are quickly selected, automatically installed, data statistics, and attached in the CATIA design environment. Non-geometric assembly information, generate 3D digital product model instead of 2D engineering drawings, automatically generate bill of materials for fasteners, and finally realize rapid design and definition of aircraft assembly, shorten product design and development cycle, and improve product design and development quality.
1. Fastener selection
The selection of fasteners is based on the mechanism of knowledge reasoning. According to the association of fasteners, the matching of fasteners is automatically selected. It is suitable for different usage scenarios, and can provide personal knowledge base, shared knowledge base, and free choice. A choice of methods, while the system supports the choice of custom fasteners.
2. Fastener installation
Once the fastener selection is determined, the system automatically calculates the fastener size based on the thickness of the laminate and automatically performs a length validity check to mount the fastener to the appropriate location. The system provides a variety of convenient wizard installation methods, including magic wand, symmetry, etc. to assist engineers in quickly completing the installation of fasteners.
3. Fastener inspection
According to the requirements of the design specifications, the system automatically calculates and checks the installed fasteners according to the specifications and requirements to confirm whether the specifications are met. It mainly includes design changes, spacing, margins, interference, installation space inspection and strength check. Figure 1 shows the gap check. The design is modified by calculations and inspections to identify non-compliant fasteners early in the design phase.Figure 1 spacing check
4. BOM statistics
Automatic calculation of fasteners and statistics, and output BOM as needed. It mainly includes fastener usage, weight, center of gravity and moment of inertia calculation; fastener clamping thickness calculation; parts list.5. Fastener database
The system provides a database of fasteners that are tightly integrated with CATIA, as shown in Figure 2, to achieve centralized classification management of fastener data, design specifications, and associated portfolio knowledge. With server and client distributed deployment, the server side centrally stores and manages all fastener information and fastener association matching definitions. The client database automatically updates data from the server database.
Conclusion
In the development of large passenger aircraft undertaken by COMAC Shanghai Aircraft Design and Research Institute, the CAFE system has been fully adopted for the design of fasteners based on full three-dimensional. In the digital assembly and manufacturing process of the prototype of the large passenger head, the system is designed and manufactured based on the full three-dimensional digital assembly, which realizes the seamless connection between design and manufacture, from the auxiliary selection of fasteners, quick transfer and implementation. Design inspection and statistical output improve work efficiency, eliminate 2D drawings, save designers' workload, shorten development cycle, reduce design cost, improve design quality, and need fasteners for several months. The Vital expression time was shortened to 2 weeks. It fully proves that CAFE system has the advantages of intelligent design, statistical automation, quick change, etc. It embodies the innovative definition of fastener association and has high promotion and application value.
Kylin Chemicals manufactures and supplies a selected range of high performance and eco-friendly biocides & disinfectants, meanwhile, provides tailored solutions to meet our customers needs at new product & technology development, problem-solving in application, and cost-reduction, etc.
There are many healthy Ingredients including glutaraldehyde low methanol,dow corning 5700,didecyl dimethyl ammonium chloride,dioctyl dimethyl ammonium chloride.
Our biocides and disinfectants are used in a variety of applications, including detergents & cleaners, indutrial cooling water treatmetn, oilfield water treatment, pool water disinfectants, aquaculature & poultry house disfection, etc.
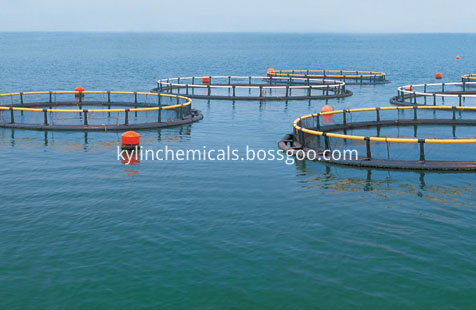
Quaternary Ammonium Biocides & Oxidizing Antimicrobials
Quaternary Ammonium Biocides,Oxidizing Antimicrobials,Benzododecinium Bromide,Benzethonium Chloride
Kylin Chemicals Co., Ltd. , http://www.kylin-chemicals.com