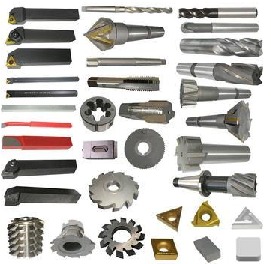
Since the milling cutter is the tool with the largest amount of metal removal in the cutting process, increasing the milling machining efficiency has become one of the innovation directions of the milling cutter. The CoroMill 345 exhibited by Sandvik Coromant is a 45° positive angle face milling cutter with a wiper blade. Compared to a standard face milling cutter with parallel-edged inserts, the table feed rate can be increased by a factor of three. And get a better surface finish. The traditional milling cutters with wiper blades are usually precision milling cutters with a small depth of cut, and the maximum depth of cut of the CoroMill 345 milling cutters is up to 6 mm. In this exhibition, Tegucico also introduced a Similar cutters. It can be predicted that the new products they exhibited will set a new benchmark for large-depth, large-feed milling cutters, which will arouse resonance and follow-up in the industry, and will be of great significance for improving the quality and efficiency of large-scale flat milling.
Promotion of new cutter structure
In this exhibition, it can be seen that some new milling cutter structures developed in recent years have been applied to more milling cutter products, and some cutter manufacturers have introduced milling cutter products with new structures in series. For example, the milling cutter that can pass the incline is first developed for the processing of mold cavity or closed groove. It has a variety of functions such as milling plane, milling cavity, milling hole, etc. It is very suitable for the characteristics of the mold processing process. Can reduce the tool change time. At this exhibition, the structural features of the milling cutter that can be ramped have been applied to various milling cutters such as face milling cutters, end milling cutters, shoulder milling cutters, and arc angle milling cutters, making most of the milling cutters The variety has the advantage of multi-functionality, not only for the mold processing, but also brings greater benefits for a wide range of conventional milling processing.
A similar situation has also appeared in the small depth of cut, large feed milling cutter, Zhuzhou Diamond Cutting Tool Co., Ltd., Tungaloy, etc. have developed a series of such milling cutters, in order to take full advantage of its large feed, increase milling efficiency . Tungaloy even applied this concept to turning tools, introducing the Turning X super-feeding turning tool that can increase processing efficiency by 8 times. Zhuzhou Diamond Cutting Tool Co., Ltd. also exhibited the newly developed FMD03, FMD04, FMP03 series of vertical bladed gravity cutting face milling cutters. The equipped LNKT series blades have positive cutting edge angles and rake angles. Less power consumption, cut depth of up to 17mm, high processing efficiency.
Improve tool economy
In order to help tool users overcome the difficulties brought about by the financial crisis, starting from the structural design of the tool and improving the economics of the tool have become one of the features of the new product development of the current milling cutter. A common practice is to design indexable inserts to be used on both sides, doubling the cutting edge. At the same time, it is also possible to increase the economy by increasing the number of edges of the polygon blade. In this exhibition, face milling cutters equipped with hexagonal, heptagonal, or octagonal double-sided inserts have become a selling point for exhibitors to promote the economics of products, such as Dijet's face milling cutters with a heptagonal blade. , and Mitsubishi's face milling cutter with an octagonal CBN insert. In addition, VARGUS's thread inserts increase the usual three tool tips to six, and are double-sided inserts that reduce the cost of the blades by more than double.
The modular interchangeable end mills exhibited by the companies not only shorten the tool change time, but also reduce the number of arbors and reduce tooling costs. A vibration-reducing tool post exhibited by the Japan Research Institute is made of a special alloy to replace the commonly used hard alloy material, which reduces the cost of the tool post.
Rapidly developing solid carbide cutters
Solid carbide end mills are also the main tools for tooling. From this exhibition, it can be seen that its main development trends are:
(1) Develop various anti-vibration milling cutters
In this exhibition, Hitachi's EPOCH MIRUS series of efficient die cutters reduced the cutting force and vibration and improved machining by optimizing the design of new glutinous rice teeth and the use of adjacent blade teeth with unequal offsets. effectiveness.
(2) Development and processing of hardened die steel milling cutters
These cutters can process material hardness ranging from HRC45-HRC67, even up to HRC70. For example, coated cemented carbide endmills (using HARDMAX coating) exhibited by Canon Inc. are suitable for high hardness of HRC45-HRC65 die steels. Processing.
(3) Development of milling cutters for machining difficult-to-machine materials
With the development of the aerospace industry and energy equipment manufacturing, the use of super alloys (including high-temperature alloys, titanium alloys, etc.) has rapidly increased, placing higher demands on processing efficiency and tool life, and also promoting new products from tool suppliers. Research and development work. For example, the CoolStar series of solid carbide end mills introduced by Mitsubishi Co., Ltd., specially designed chip flutes improve the chip evacuation effect, and set multiple internal cooling holes in each flutes to improve the cooling effect. In combination with the use of high toughness matrix materials with good wear resistance, efficient machining of super alloy materials can be achieved and tool life can be extended. OSG has exhibited an end mill developed for the aerospace industry to process composite materials. The milling cutter has a special groove shape that prevents delamination and formation of burrs when processing multi-layer composite sheets.
(4) Development of milling cutters for processing graphite and aluminum alloys
Such tools use a diamond or diamond-like coating to provide powerful technical support for highly efficient processing of graphite electrodes and aluminum alloys. For example, the rake face of the aluminum alloy roughing cutter exhibited by OSK company has an oblique swarf groove, which makes the cutting lighter and prevents chip sticking and makes the tool life longer.
Tool Application Guide
It is worth mentioning that at this exhibition, Sandvik Coromant distributed two brochures for “milling application guides†to visitors, including the selection of milling cutters, the setting of milling parameters, and the correct path Paths and implementation plans. With the increasing popularity of CNC machine tools, traditional milling methods can no longer meet the requirements of CNC milling, which greatly restricts the full play of the performance of CNC machine tools. This kind of comprehensive and systematic introduction of modern milling techniques and practical application of the booklet to the promotion of modern milling processing technology for the advancement and popularization of applications, improve the milling process technology and social and economic benefits of great value, will have a profound impact. At the same time, the technical guide manuals displayed at the exhibition included turning, milling, drilling, boring and shank handles, etc., and comprehensively introduced the application of new technologies for modern cutting tools. The value of these technical materials for a large number of tool users far exceeds a new tool exhibit, which has become a highlight of this exhibition and should arouse the attention of tool users.
Carbon Additives,Steel Making Carbon Additive,Carbon Additives Anthracite,Best Carbon Additives
Ningxia Jinyihui Environmental Protection Technology Co., Ltd. , http://www.chinajyhhb.com