The airflow drying device is only applied to the powdery granular material, and the dried material is directly fed into the airflow drying device by the feeder, and the air is sent to the combustion furnace by the air blower, and after heating, enters the bottom of the airflow drying device. The high-speed hot gas stream accelerates and disperses the added granular wet material to be suspended in the gas stream, and completes the drying of the wet material during the acceleration and transportation of the gas stream. If a wet material disperser or a small material pulverizer is added to the air drying apparatus, the apparatus can also be used for drying the filter cake material and the bulk material.
The main feature of the airflow drying equipment in drying materials is that since the dried material is dispersed and suspended in the airflow, the entire geometric surface area of ​​the material participates in heat transfer and mass transfer, so effective heat transfer, mass transfer area, volumetric heat transfer The coefficient is high, generally 2326-6978W / (m?. °C). In the design of some airflow drying equipment, the volumetric heat transfer coefficient is 1163-3479W/(m?.°C) for materials containing non-bonded moisture, and the volumetric heat transfer coefficient is 582-1163W/(for porous materials containing combined moisture). m?.°C); For a dispersing machine with highly dispersed materials in the process, the volumetric heat transfer coefficient is 3479-11630W (m?.°C). After the air-dried material, the unbound water can be almost completely removed, such as residual moisture in the crystalline salt product is about 0.3%-0.5%, and for the highly adsorbable material, the residual moisture in the product is about 2%- 3%. The drying operation of the airflow drying equipment has a large airflow speed. Generally, for materials with good dispersibility, the operating gas velocity is 10-40 m/s, so the residence time of the materials in the drying equipment is short, generally about 0.5-2 s, and the longest can be Up to 7s. The temperature of the material outflow drying device is close to the wet bulb temperature of the air of about 60-70 ° C. Therefore, the air flow drying device is suitable for drying the heat sensitive material. The structure of the airflow drying device is simple, and the airflow drying device currently used has a drying pipe height of 6-20 m and a pipe diameter of 0.3-1.5 m. The air drying tube like dry 2.5*(10*10*10*10) Kg/h coal or 1.5*(10*10*10*10) Kg/h ammonium sulfate has a diameter of 0.7 m and a height of 15 m. Large production capacity. Like treatment of quartz sand 2.5** (10 * 10 * 10 * 10) Kg / h, urea 6.0** (10 * 10 * 10 * 10) Kg / h. The heat dissipation area of ​​the airflow drying device is small, and the heat loss can be controlled at about 5%. Therefore, the thermal efficiency is high, and the thermal efficiency can reach 60%-75% when the hot air temperature is above 400 °C and the exhaust gas discharge temperature is 60-100 °C. However, when the moisture is combined in the dry material, the thermal efficiency is about 20% due to the lower air temperature of the drying device. The airflow drying equipment has a small main equipment, low equipment investment cost, small floor space, continuous operation, and easy automatic control. However, the accessory equipment of the airflow drying equipment is large, the operating air velocity is high, the material under the action of the airflow, the impacting of the pipe wall, and the collision between the materials, the wear of the materials and the pipe is large, and the requirements for the granularity and the crystal form are very strict. The drying equipment should not be used for materials.
Secondly, airflow drying equipment is also not suitable for highly adherent materials. In addition, it is not suitable to use the drying equipment for drying materials which are easy to produce fine powder during the drying process and which are not suitable for separation, and materials which require a large amount of air.
At present, there are many small and medium-sized airflow drying equipments in China, and there are fewer large-scale airflow drying equipments; there are many processes using direct feeding, and there are fewer processes using other auxiliary devices. However, there have been many developments in the modification and strengthening of the drying tubes of airflow drying equipment, such as pulse type, cyclone type, push cone type airflow drying equipment.
Through this introduction, do you have a new understanding and understanding of airflow drying equipment, which can increase the unnecessary waste of resources and low product quality in the use of airflow drying equipment, and also solve the problem that airflow drying equipment can be applied to What material, and the problem of blind use.
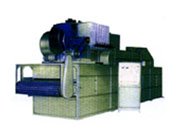
1. Product introduction
Coal-based columnar net gas Activated Carbon is cylindrical, tasteless non-toxic; as high quality anthracite the raw material, by process of crushing, mixing, extrusion, molding, drying, carbonization, activation and made. It has reasonable pore structure, good adsorption properties, high mechanical strength, able to withstand the high temperature, high pressure and not easily broken, easy to regenerate, and low cost characteristics. It is widely used in sewage treatment, gas treatment, solvent recovery, desulfurization and denitrification, nitrogen making machine, air separation equipment, paint shop and other fields.
2. Application
a.Coal columnar net gas activated carbon used for purification, such as chemical raw materials, pharmaceutical chemical synthesis gas, industrial gas, nitrogen, chlorine, hydrogen chloride, ethylene hydrocarbons, ozone, ethane, butane, cracking gas, carbon dioxide and hydrogen used in beverage; atomic facilities exhaust inert gas and remove the pollutants; also separate and purify mixed gas. It also can be used for gas masks and protective equipment disinfection and filtration.
b.Coal columnar net gas activated carbon is mainly suitable for industrial waste treatment, such as waste gas power plant, chemical plant gas, coking plant, smelting plant, oil plant. Coal columnar net gas activated carbon rely on the good adsorption capacity, developed gap, high iodine value can make a cleaning purpose.
3. Adsorption purification principle and process
The physical properties of coal-based activated carbon introduction: it is cylindrical black particles; the physical, chemical properties analysis of carbon is a porous carbon, the highly developed pore structure makes it has large surface area, so it is easy to full contact with toxic and harmful gases in the air (and harmful impurities), so this highly developed capillary and pore structure formed a powerful adsorption force field, which gives the unique adsorption properties of activated carbon.
Adsorption: the organic waste gas passes through the filter removed the solid particulate material, from the upper to the lower into the adsorption tank. The organic matter is captured, absorbed and concentrated by the activated carbon, and the purified air is discharged from the lower part of the tank through the main fan into the atmosphere.
Stop: when activated carbon adsorption reached saturation,it stops to inhalation waste gas; and then blowing up into the steam through the activated carbon bed, which expelled the organic matter from the activated carbon, and the subsequent restoration of desorption, activated carbon activity is recycled.
Hot air drying and cooling: the activated carbon layer after desorption remains 80%-90% steam condensate which can in reducing carbon layer activity; therefore using the hot air to dry, close the steam valve, and then through the air cooling at 25 DEG C, activated carbon can be recovered into the circulation.
Columnar Net Gas Activated Carbon
Columnar Net Gas Activated Carbon,Columnar Activated Carbon,Pellet Activated Carbon For Gas Mask
Ningxia XingKai Silicon Industry Co., Ltd. , http://www.xingkaisic.com