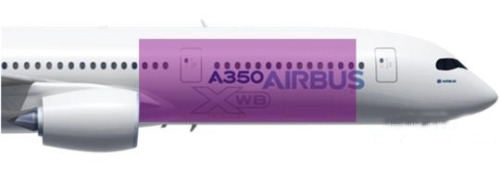
Airbus uses a large fuselage panel in the Airbus A350XWB, which can be designed to different thicknesses according to the different weights the body needs to withstand. This method can optimize the body as a whole to improve performance and stiffness while reducing weight.
Chinese companies participate in Airbus A350XWB manufacturing and design
The 5% manufacturing of Airbus' latest model A350XWB widebody aircraft will be completed in China. A number of Chinese companies are responsible for the manufacturing of key components of the Airbus A350XWB. Among them, Harbin Hafei Airbus Composite Material Manufacturing Center will undertake the manufacture of composite parts such as A350XWB rudder, elevator, 19-section maintenance doors and belly cowling. Chengfei Civil Aircraft Co., Ltd. undertakes the manufacture of spoilers and drop plates for the A350XWB widebody aircraft. The Airbus (Beijing) Engineering Technology Center participated in the design of the A350XWB. The Airbus A350XWB project not only embodies “Made in China†but also reflects “Created in Chinaâ€.
Airbus A350XWB project production event
In 2010, the Airbus A350XWB widebody aircraft project entered the production phase. The production of the Airbus A350XWB has made remarkable progress in Airbus and its partner factories located around the world.
Among the productions made at the Airbus plant include the production of A350XWB wing panels and rear fuselage barrels at the Aires Illescas plant in Spain; production of the wing top panels at the Stade plant in Germany; South of France The assembly of the central wing box and the production of the keel beam were carried out at the special factory; in the Felton, UK, the A350XWB landing gear system test facility was started.
Production at the Airbus partner plant includes a 19.7 meter long composite central fuselage top panel manufactured by Spirit AeroSystems, Inc., North Carolina, USA at its subsidiary in Kingston, and Premium Aerotech, located in Nordenham, Germany. Finished curing of upper fuselage section panel.
About Airbus A350XWB Widebody Aircraft Series
The Airbus A350XWB widebody aircraft series consists of three passenger aircraft with true long-distance transport capabilities and a range of up to 8,500 nautical miles/15,580 kilometers. With a typical three-class passenger cabin layout, the A350-800 can carry 270 passengers and the A350-900 and A350-1000 can carry 314 and 350 passengers respectively. In the high-density layout, three models can be deployed to 440 seats. The design of A350-900, the basic model of the A350XWB wide-body aircraft series, was frozen in December 2008 and is progressing smoothly. It will be put into operation as planned in the second half of 2013.
Sintered Saw Blade Co., Ltd. , http://www.nsdiamondtool.com